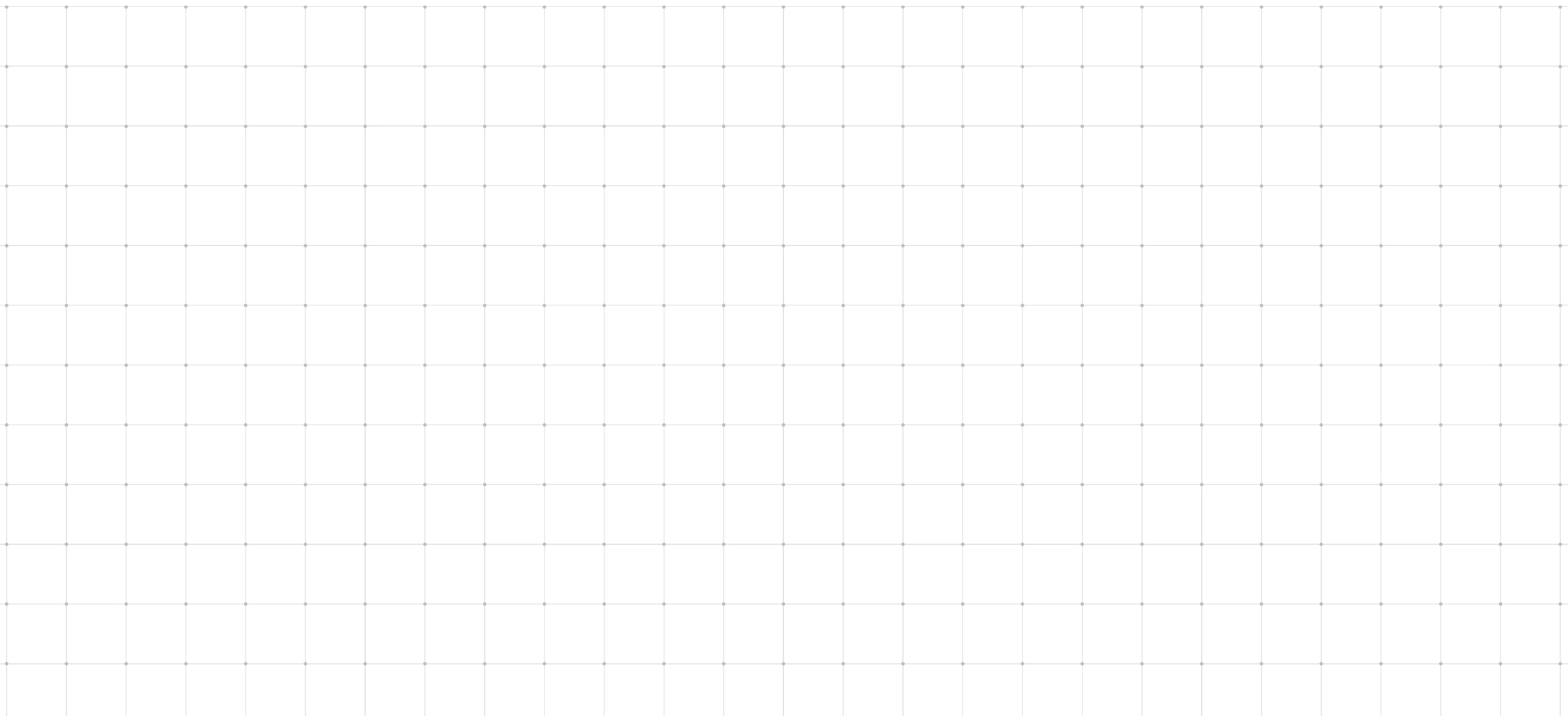
Why Cold Storage Facilities Must Prioritize Efficiency
When it comes to cold storage facilities, they’re responsible for the preservation and storage of everyday items we wouldn’t even think of, making them an essential part of day-to-day life that is often overlooked. As temperatures inside need to be kept low, sometimes below freezing, it’s imperative that they’re built with efficiency in mind so interior temperatures can be isolated effectively.
How Thermal Breaks Help Reduce Energy Consumption
Substantial energy is needed to help maintain cool temperatures inside these facilities, which can result in costly bills for owners. To attempt to reduce the amount of energy needed to prevent temperature fluctuations, thermal breaks can be incorporated within the build stage at any application where the continuous insulation is interrupted.
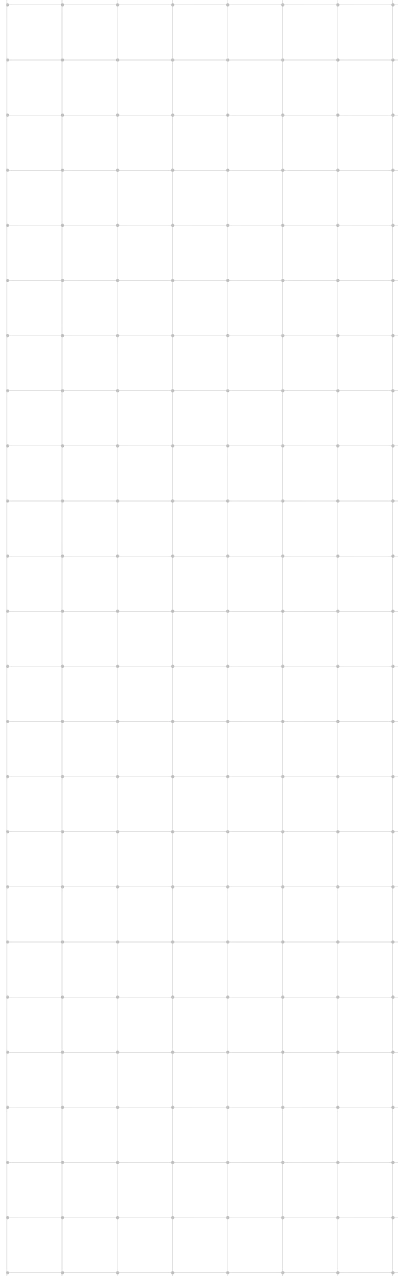
Why Hardwoods Fall Short in Cold Storage Applications
The main concern was bridging between the building columns and the slab insulation, and sourcing a solution which could support the desired load. With the future of the structure in mind, hardwoods had been dismissed – although previously used within thermal bridging locations, they can absorb moisture over time. If the timber does become damp, the insulation is reduced and there’s a high risk of rotting which can put the integrity of the building at risk.
How Armatherm 500 Prevents Thermal Bridging at Column Bases
Our team provided an alternative that didn’t harbor these disadvantages, and also provided additional benefits. The makeup of our materials mean they won’t wick moisture, allowing the insulation performance to continue throughout the lifetime of the building. Armatherm 500 was installed directly under the steel column bases which bridge the floor slab insulation. Support columns pass through the non-load bearing slab insulation to warm ground beneath, short circuiting the insulation barrier and transferring warmer temperatures into the building.